1. Introduction:
Through the first phase of the study, it was found that laser shock peening (LSP) can produce a large density of dislocations near the surface of the material. These dislocations are expected to become the nucleation points of the precipitated phase of the material during the heat treatment. Therefore, this part of the research to study the precipitation behavior was carried out. It is hoped that the control of precipitation behavior can be achieved through LSP.
2. Details of the research
The material selected in this experiment is aluminum alloy 7050-T7451 that can be strengthened by heat treatment. The original state of the material T7451 is a fully aged state, so in this experiment, it is firstly solution treated. After that, the experiment was divided into two parts. The first part was heat treatment after double-sided LSP of the thin plate, and the tensile properties in each different state were tested; the second part was the single-sided LSP on the thick plate, and then the residual stress and microstructure were characterized in depth.
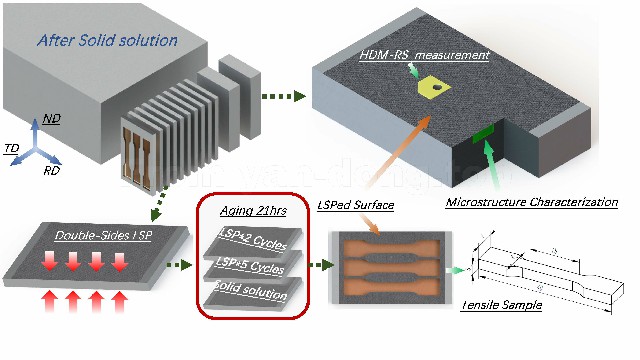
This is a heat treatment method selected according to international standards, which is quenched after solid solution and two-stage aging treatment. LSP is performed after quenching.
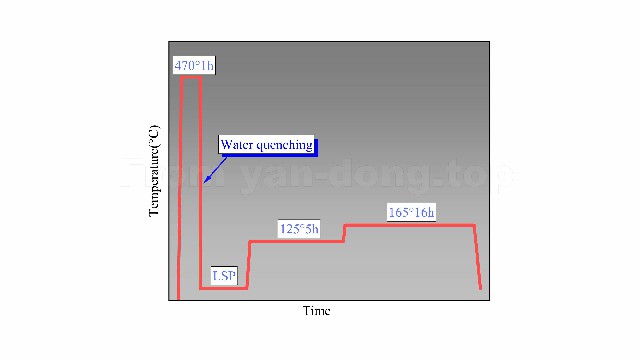
The residual stress test results show that the near surface of the material in the original state is tensile residual stress, which is converted into a small amplitude residual compressive stress after solution and quenching. LSP produces a higher magnitude residual compressive stress in the near-surface area, and the residual stress still exists in the near-surface area after solid solution.
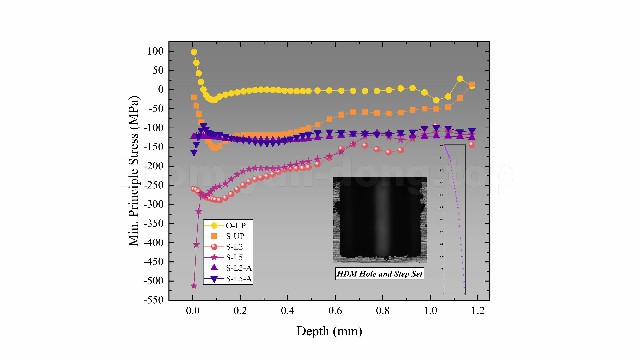
This is the change of electrical conductivity after heat treatment and LSP. After the solution treatment, the conductivity decreased significantly, and with the increase of the number of LSP treatments, it dropped slightly. After solution treatment, the conductivity of the sample treated with LSP is significantly higher than that of the material without LSP treatment, which shows that the LSP treatment effectively increases the density of the precipitated phase.
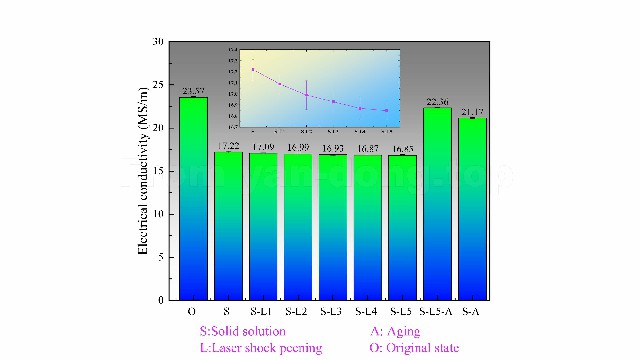
The figure below is the curve and statistical data of tensile test. After solution treatment, the strength of the material is significantly reduced, but the elongation is greatly increased. After aging, the strength increased significantly. Among them, the sample without LSP treatment has the highest strength but the lowest elongation rate, while the sample after LSP treatment has a higher elongation rate and the strength is closer to the original T7451 state. This phenomenon is determined by the unique precipitation behavior of 7050 aluminum alloy. In the two-stage aging treatment, the first-stage low-temperature aging can increase the strength but greatly reduce the elongation; the second-stage high-temperature aging sacrifices a small part of the tensile strength and yield strength in exchange for better elongation and corrosion resistance, thereby improving the overall performance of the material. Therefore, the tensile data shows that the performance of the sample after LSP treatment is closer to the original state after sufficient aging, which illustrates the promotion effect of LSP on the precipitation behavior.
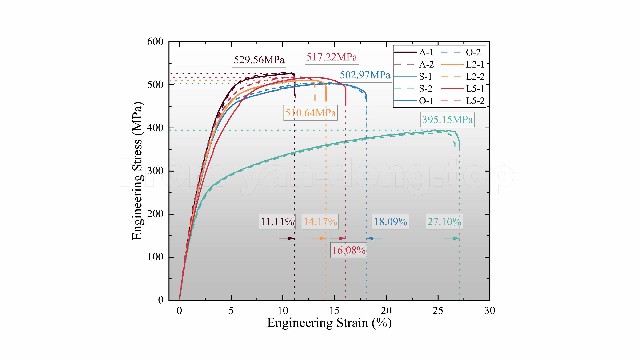
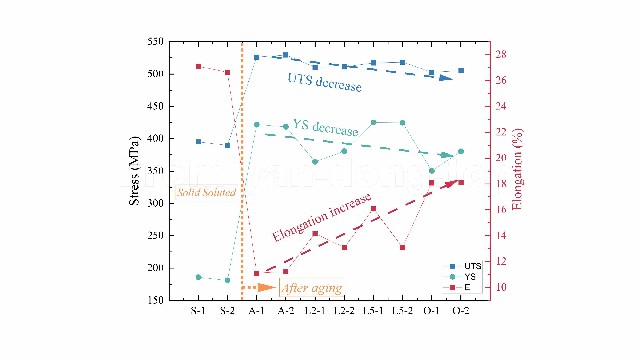
P.S.
Since the experimental results described in this article have not yet been published, it is not appropriate to release the results of microstructure characterization here. If you are interested in my research, please send an email to me, I will be very glad to contact you!
My basic experiment on LSP includes the first part and the second part (this article). This is the entire content of my basic experiment. In the future, I will conduct experiments that combine LSP and additive manufacturing.